What Is A Helicopter Blade Called
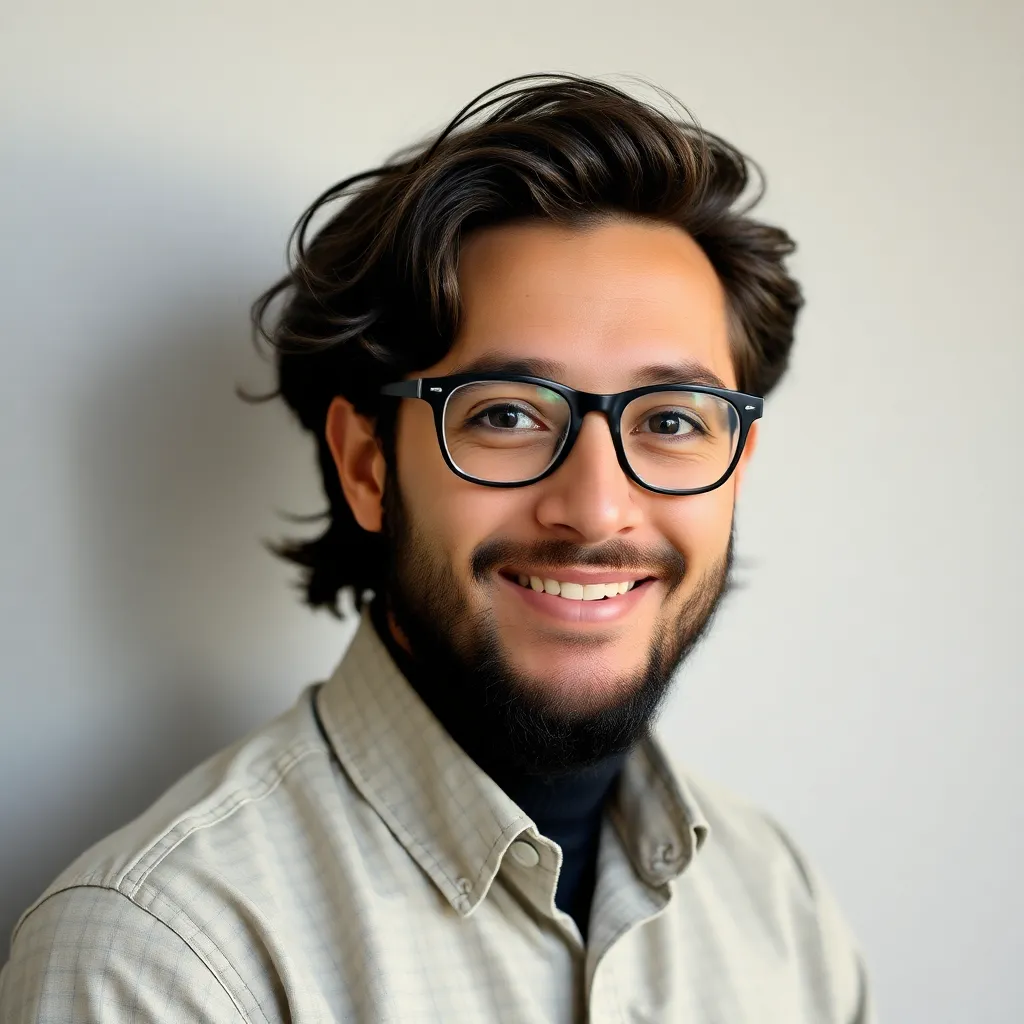
Espiral
Apr 24, 2025 · 6 min read

Table of Contents
What is a Helicopter Blade Called? A Deep Dive into Rotorcraft Technology
Helicopters, those marvels of vertical flight, owe their unique capabilities to a crucial component: the rotor blades. But what are these whirling wonders actually called? While colloquially referred to as simply "blades," the technical terminology is richer and more nuanced, revealing the intricate engineering behind these essential parts. This article delves into the specifics, exploring the various names, their functionalities, and the sophisticated technology that makes them work.
Understanding the Nomenclature: Beyond "Blade"
The term "blade" is certainly the most common and widely understood descriptor. However, the aviation industry employs more precise and descriptive terminology depending on the context and specific application. You'll often encounter terms like:
-
Rotor Blades: This is the most encompassing term, referring to all the blades collectively attached to the rotor hub. It's a broad categorization that encapsulates all aspects of the rotating assembly.
-
Rotating Blades: This emphasizes the dynamic nature of the component, highlighting its constant motion during flight. It's useful when discussing the aerodynamic forces generated by the rotation.
-
Airfoils: This term highlights the aerodynamic shape of the blade, crucial for generating lift. The airfoil design is meticulously engineered to maximize efficiency and control.
-
Rotor Wings: This term underscores the wing-like function of the blades, producing lift in a similar fashion to fixed-wing aircraft, albeit with a rotating system.
-
Main Rotor Blades: This specifically differentiates the blades of the main rotor system from those of a tail rotor. The main rotor is responsible for the helicopter's primary lift and forward/backward movement.
-
Tail Rotor Blades (Anti-torque Blades): These blades are smaller and mounted at the tail, countering the torque generated by the main rotor and controlling yaw (rotation around the vertical axis). They are also sometimes called anti-torque blades.
The Anatomy of a Helicopter Blade: A Closer Look
A helicopter blade isn't just a simple piece of metal or composite material. It's a highly engineered component with several key features:
1. Airfoil Section:
The cross-sectional shape of the blade is designed as an airfoil, similar to the wings of a fixed-wing aircraft. This shape generates lift when air flows over it, a critical function for vertical flight. The airfoil's curvature, thickness, and camber (the degree of curvature) are meticulously calculated and optimized for the specific helicopter design and operational conditions. Different airfoil sections might be used along the span of the blade to optimize performance across various speeds and flight regimes.
2. Blade Spar:
The blade spar is the main structural element of the blade. It's typically a strong, lightweight material, like a composite material (carbon fiber, fiberglass, or kevlar) or a strong metal alloy, that provides the necessary stiffness and strength to withstand the significant stresses of rotation and aerodynamic forces. The spar runs along the length of the blade and acts as its backbone.
3. Blade Skin:
The blade skin is a thin outer layer, usually made from composite materials, that covers the spar and other internal components. It contributes to the overall aerodynamic shape and smoothness of the blade. This smooth surface minimizes drag and maximizes lift generation. The design of the skin also plays a role in reducing noise during operation.
4. Trailing Edge:
The trailing edge is the rear edge of the airfoil section. Often, the trailing edge features a flexible flap or hinge, which can be adjusted (actively or passively) to control blade pitch and optimize performance during different flight maneuvers. This adjustment is crucial for achieving precise control and stability. These adjustments are critical for controlling lift, drag, and pitch.
5. Leading Edge:
The leading edge is the front edge of the airfoil section. This part of the blade is often reinforced to withstand impact with debris, birds, and other hazards encountered during flight. The leading edge design can also influence the noise generated by the blade during flight. The leading edge's design has a significant impact on the blade’s aerodynamic performance and efficiency.
6. Blade Tip:
The blade tip is the outermost portion of the blade, traveling at extremely high speeds during flight. The design of the blade tip is crucial for minimizing noise and drag. Various designs exist, including swept tips and curved tips, that aim to reduce noise levels and improve overall aerodynamic efficiency.
7. Pitch Link:
This is the mechanism that connects the blade to the rotor hub, allowing for the adjustment of the blade's pitch angle. This adjustment is controlled by the pilot and enables precise control of the helicopter's attitude and maneuverability. Different types of pitch links offer various levels of sophistication and control.
Different Types of Helicopter Blades:
While the fundamental components remain similar, different types of helicopter blades exist, each optimized for specific performance characteristics:
-
Articulated Blades: These blades have hinges that allow them to move independently during flight, accommodating variations in airflow and preventing excessive stress on the rotor hub. This flexibility is crucial for maintaining stability and efficiency throughout the entire rotational cycle.
-
Rigid Blades: Unlike articulated blades, rigid blades do not incorporate hinges. This design prioritizes simplicity and weight reduction. However, the absence of hinges necessitates greater structural rigidity and careful design considerations to withstand the cyclical stresses of rotation.
-
Bearingless Blades: These are increasingly prevalent in modern helicopter designs and feature a design that eliminates the need for traditional blade pitch bearings. This enhances efficiency and reduces maintenance. The pitch mechanism is often integrated into the blade structure itself.
Materials Used in Helicopter Blade Construction:
The choice of materials for helicopter blades is critical. They must be strong, lightweight, and resistant to fatigue and extreme stresses. Common materials include:
-
Aluminum Alloys: Historically a dominant material, aluminum alloys offer a good balance of strength and weight. However, composites have increasingly superseded them due to superior performance.
-
Composite Materials: These are now the preferred choice for many modern helicopter blades, offering high strength-to-weight ratios, excellent fatigue resistance, and the ability to be molded into complex shapes. Carbon fiber, fiberglass, and kevlar are frequently used components in these advanced materials.
The Importance of Blade Maintenance:
The helicopter's blades are critical for safety and performance. Regular maintenance, inspections, and thorough checks for damage are absolutely paramount. Any damage or wear can significantly compromise the integrity of the blade and the safety of the helicopter and its occupants. This maintenance involves visual inspections, non-destructive testing, and potentially repairs or replacement.
The Future of Helicopter Blades:
Continuous research and development are ongoing, focused on improving the efficiency, noise reduction, and overall performance of helicopter blades. Advancements include:
-
Advanced Materials: The use of more sophisticated composite materials and advanced manufacturing techniques aims to create even lighter, stronger, and more efficient blades.
-
Active Twisting Mechanisms: These allow for more precise control of the blade's pitch along its length, leading to enhanced maneuverability and stability.
-
Noise Reduction Designs: This area is crucial for reducing the environmental impact and improving the acceptability of helicopters. Research includes innovative blade tip designs, advanced airfoil shapes, and noise-canceling techniques.
In conclusion, while the common term for a helicopter's spinning component might be "blade," the reality is far more complex. Understanding the nuances of terminology—from rotor blades and airfoils to main rotor blades and tail rotor blades—provides a richer appreciation for the intricate engineering involved in these critical flight components. The continuous evolution of materials, design, and manufacturing techniques promises to push the boundaries of helicopter performance, efficiency, and noise reduction in the years to come.
Latest Posts
Latest Posts
-
Inside The Pyramids Of Egypt Pictures
Apr 25, 2025
-
Pros And Cons Of The Louisiana Purchase
Apr 25, 2025
-
Hot Air Balloon When Was It Invented
Apr 25, 2025
-
Where Is The Bowery In Nyc
Apr 25, 2025
-
What Is The River That Runs Through Amsterdam
Apr 25, 2025
Related Post
Thank you for visiting our website which covers about What Is A Helicopter Blade Called . We hope the information provided has been useful to you. Feel free to contact us if you have any questions or need further assistance. See you next time and don't miss to bookmark.